The AC 800M controller is exceptionally open and scalable. It is easy to connect to the surrounding world of supervisory systems and intelligent devices of all kinds, and it is adaptable to changing requirements as the process it controls changes or expands.
Wide-ranging control functionality is available for process, electrical, turbomachinery, and safety.
AC 800M Process and High Integrity Controllers
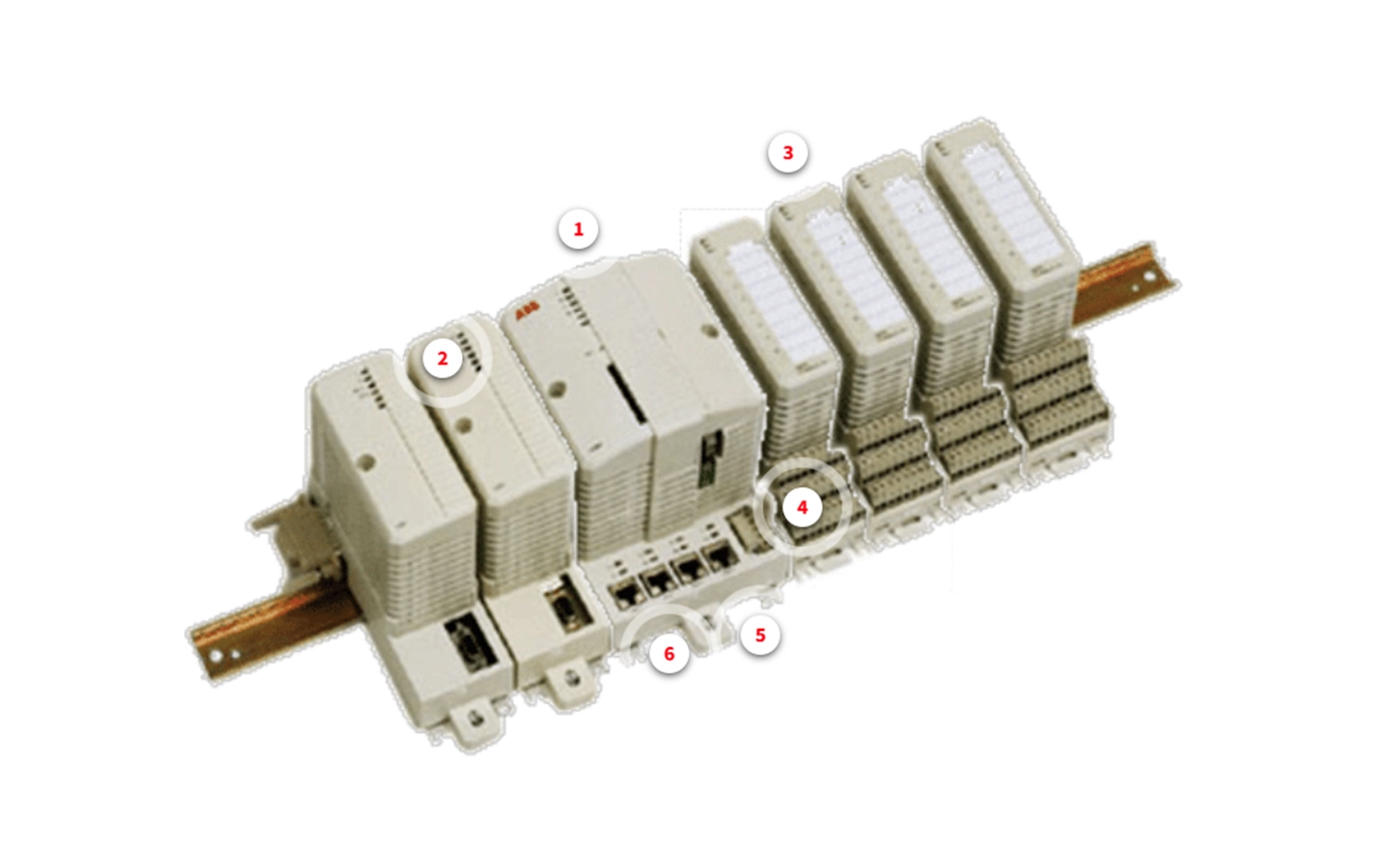
The AC 800M controller consists of a selection of units mounted on horizontal or vertical DIN-rails:
- Processor Unit ①
- Communication interface modules for different protocols (max 12 on CEX-Bus) ②
- S800 I/O modules (max 12 on Electrical Module Bus) ③
- Power supply units ④
The Processor Unit consists of a base plate TP830 and a replaceable processor module PM8xx with various speed and memory combinations. The memory is backed up by internal or external rechargeable battery.
The Base plate TP830 carries the connections to the processor module, the power supplies, the communication interfaces, as well as the external buses.
Each Processor Unit is equipped with two Ethernet ports ⑥ for communication with other controllers on the control network and two serial ports ⑤ for diagnosis. A compact flash memory card can be inserted into a slot in the Processor Unit to store the application.
AC800M can easily be configured for use in safety critical applications. The main components are the supervisory module SM812 and the processor module PM867 running a high integrity version of a control software in combination with S800 I/O High Integrity.
In a system with redundant processors, the controller contains two Processor Units linked together with the RCU Link Cable. One unit is acting as primary, while the other is backup (hot stand-by). The primary unit controls the process. The backup unit stands by to take over in case of a fault in the primary unit. The primary unit is always updating the backup unit, and the changeover is done in less than 10ms.
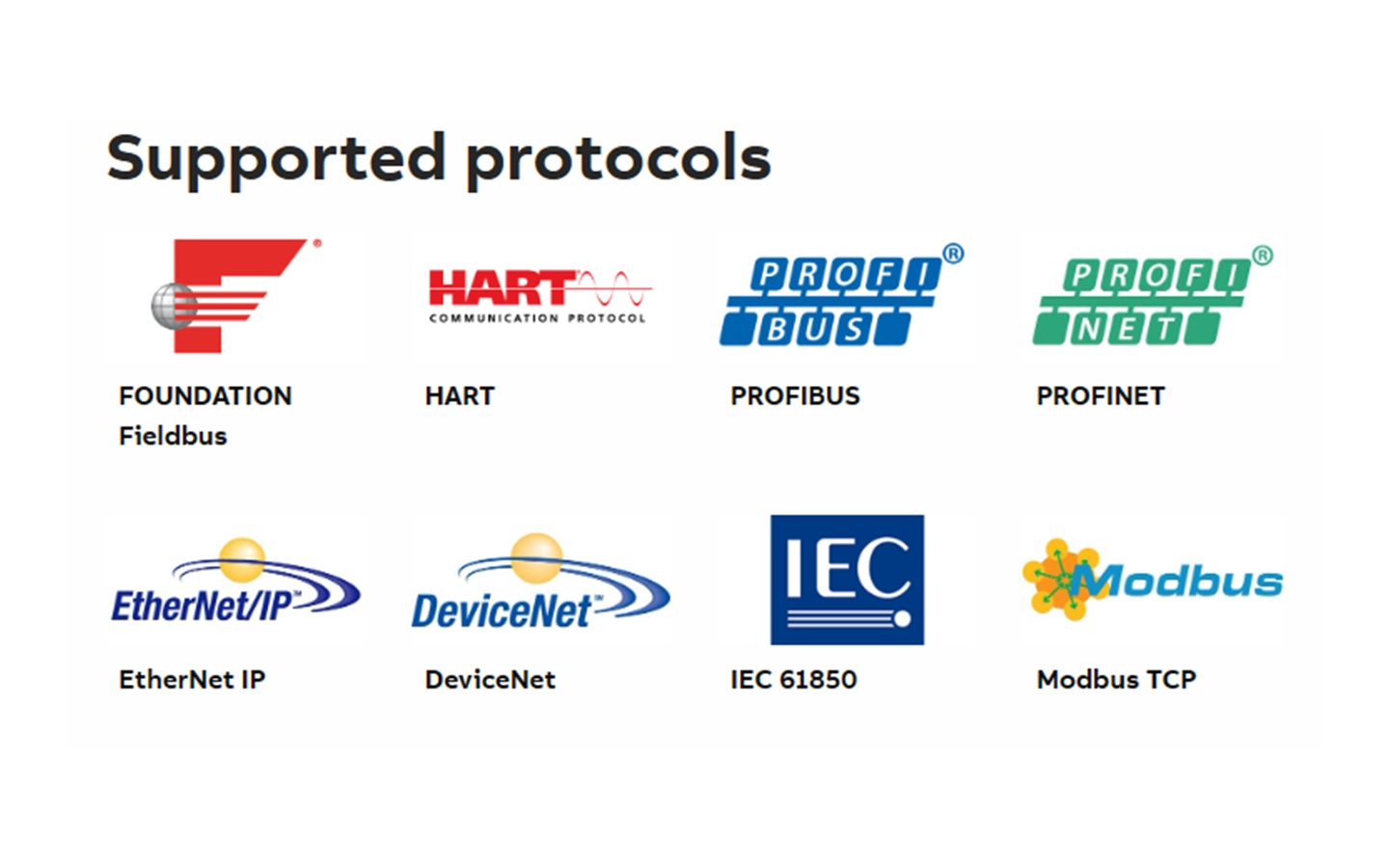
DCS-ECS-HI Integration
The Distributed Control System (DCS) is the central brain of a plant and controls all aspects of the process.
The fully integrated Electrical Control System (ECS) enables control of the complete electrical system, from high-voltage switchgear to low-voltage motor control. Complete substation information is brought to the control room enabling proactive action and appropriate decisions.
Better visibility into power consumption and real-time energy usage delivers a clear picture of the energy distribution throughout the plant.
The High Integrity Safety System (HI) is TÜV certified for SIL3 and provides a wide range of field proven applications, including Fire & Gas (F&G), Emergency and Process Shutdown (ESD & PSD), interlock systems, Burner Management and Boiler Protection (BMS), critical control, High Integrity Pressure Protection Systems (HIPPS) and Pipeline Protection Systems (PPS).